About Caldera Engineering
About Caldera
High Pressure Acid Leach
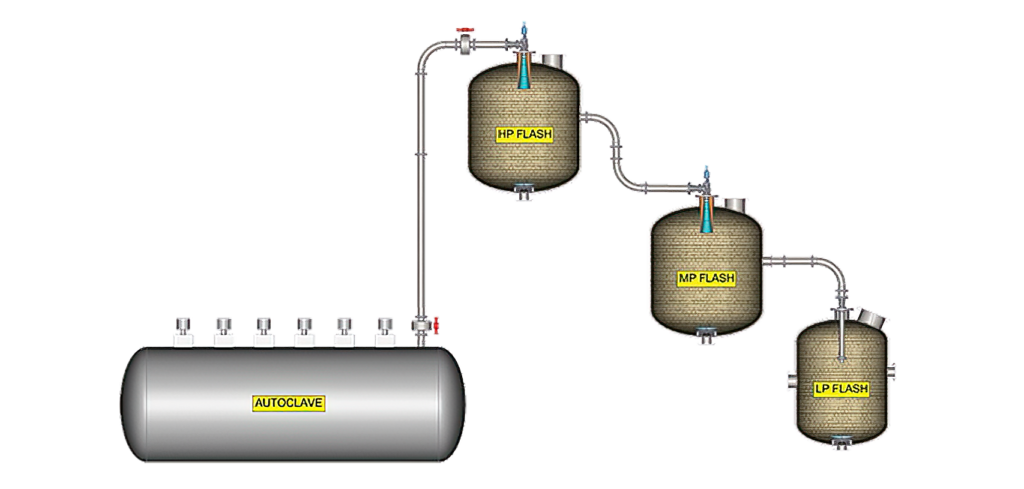
Overview
High Pressure Acid Leach (HPAL) is a process used to extract nickel and cobalt from laterite ore bodies. The HPAL process utilizes elevated temperatures (roughly 255 degrees Celsius), elevated pressures (roughly 50 bar or 725 psi), and sulfuric acid to separate nickel and cobalt from the laterite ore.
HPAL has been used since 1961 when it was first put into commercial production at Moa Bay, Cuba. It has subsequently increased in use since that time.
How It Works
The HPAL process works as follows: ore is mined and crushed to create a fine material. These fines are mixed with water to create a slurry which is then preheated. This hot slurry is pumped into an autoclave (a giant pressure cooker of sorts) where acid is added. The slurry and acid then react as they flow through several compartments within the autoclave. The slurry takes approximately 60 minutes to complete the leaching process in the autoclave. Upon leaving the high pressure and temperature atmosphere of the autoclave the slurry must be returned to atmospheric conditions. This is accomplished through two or more letdown/flash stages. Once the slurry is at atmospheric conditions it is washed and separated at which point the nickel and cobalt can be recovered from the liquid fraction.
The Benefit
The major benefit of HPAL is the ability to quickly leach nickel and cobalt from laterite ores. Traditional leaching methods are more time-intensive and result in lower recoveries.
The Challenges
Some of the challenges of HPAL are:
- Corrosion and Erosion
- Autoclave Level Control
- Operating and Maintenance Procedures
- Plant Availability
- Energy Requirements
If you are designing or operating an HPAL, POX, or other pressure hydrometallurgy plant and have questions about pressure letdown equipment, please call us at +1 801-356-2862.